The Growing Importance of Rapid Prototype Plastic in Modern Manufacturing
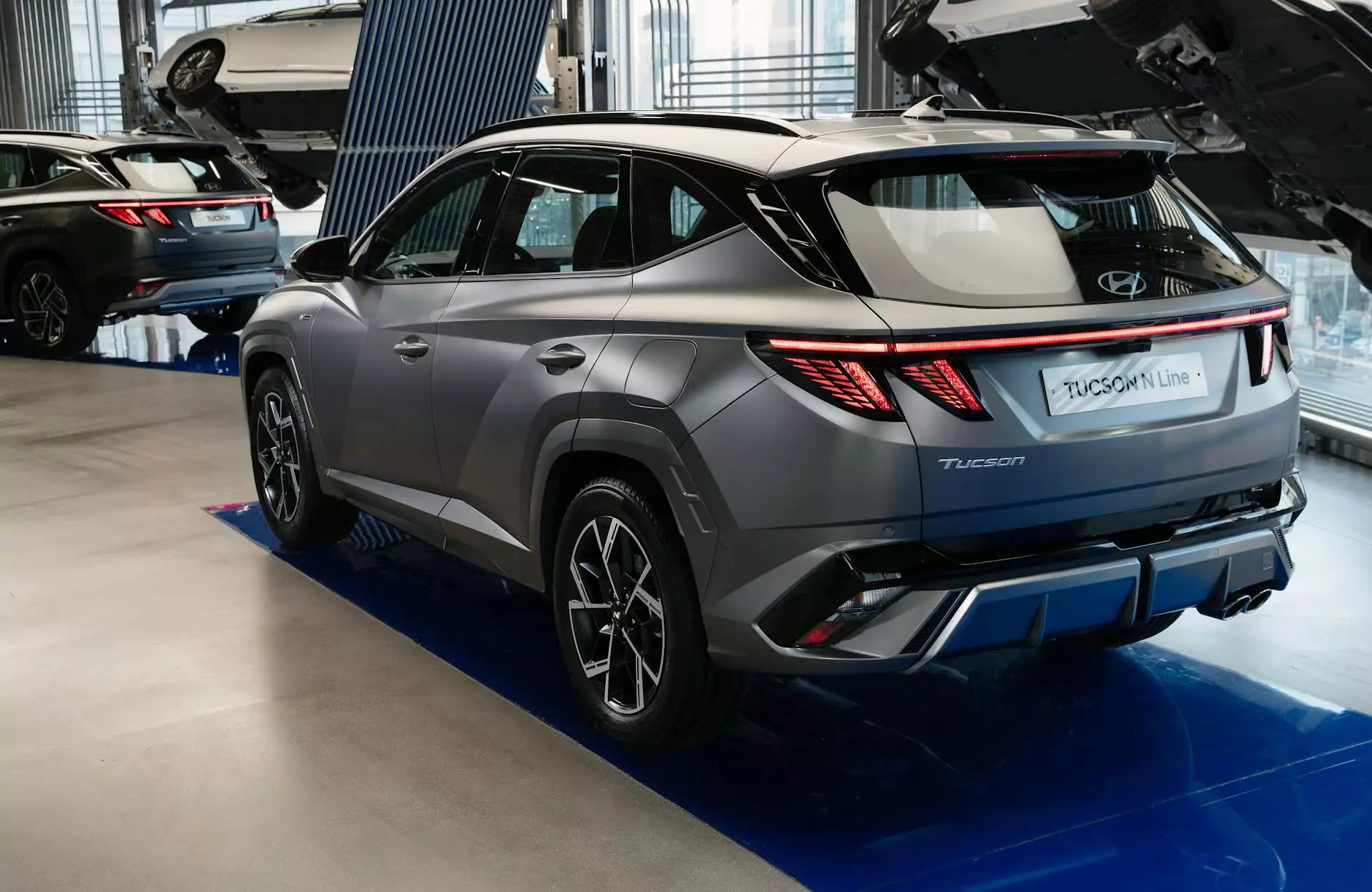
In today’s fast-paced manufacturing landscape, the need for speed and precision has never been more critical. This is where rapid prototype plastic comes into play. The process of creating prototypes rapidly has revolutionized how products are designed and manufactured, leading to increased efficiency, reduced costs, and enhanced creative freedom. In this article, we delve deeply into the world of rapid prototyping, its benefits, applications, and the role of expert services like Deep Mould in the metal fabrication sector.
Understanding Rapid Prototyping
Rapid prototyping refers to the quick fabrication of a physical part, model, or assembly using 3D computer-aided design (CAD) data. Often associated with additive manufacturing or 3D printing, this technique allows designers to bring their ideas to life faster than traditional methods. The choice of material is crucial in this process, with rapid prototype plastic being one of the most popular options due to its versatility and ease of use.
Benefits of Using Rapid Prototype Plastic
- Speed: The primary advantage of rapid prototyping is the dramatically reduced time to produce prototypes. Traditional methods could take weeks or even months, while rapid prototype plastic can be produced in days or even hours.
- Cost-Effectiveness: By identifying issues early in the design phase using rapid prototypes, businesses can save significant resources on production costs.
- Flexibility: Designers can easily modify and adapt their prototypes, allowing for enhanced innovation and creativity.
- Realistic Representation: Prototypes made from plastic can closely resemble the final product, providing valuable insights into aesthetics and functionality.
Applications of Rapid Prototype Plastic
Rapid prototype plastic has diverse applications across various industries. Here are some of the most noteworthy:
1. Product Design and Development
In product design, the ability to create realistic prototypes quickly allows designers to test form, fit, and function efficiently. This iterative process is essential for consumer goods, electronics, and automotive components.
2. Medical Device Manufacturing
The medical industry relies heavily on rapid prototyping for developing devices and instruments that demand high precision. Prototypes are vital for testing ergonomics, usability, and functionality before mass production.
3. Aerospace and Automotive Sectors
In aerospace and automotive manufacturing, weight and efficiency are paramount. Rapid prototype plastic helps engineers create lightweight components that can be tested in aerodynamic conditions.
4. Architectural Models
Architects utilize rapid prototyping to create scale models of structures. These models aid in visualizing projects and communicating ideas to clients and stakeholders effectively.
Technology Behind Rapid Prototype Plastic
The technology of rapid prototyping has evolved significantly, enabling a wide range of materials and methods. Some of the most prevalent techniques include:
- Fused Deposition Modeling (FDM): This method extrudes heated thermoplastic filament to build models layer by layer. It is one of the most common techniques for rapid prototyping due to its accessibility and cost-effectiveness.
- Stereolithography (SLA): SLA uses a laser to cure liquid resin into hardened plastic. This process creates highly detailed and accurate prototypes and is often used for producing complex geometries.
- Selectively Laser Sintering (SLS): In SLS, powdered materials are fused together using a laser, allowing for intricate and sturdy prototype structures that can withstand functional tests.
- Digital Light Processing (DLP): Similar to SLA but utilizes a digital light projector, making it faster and suitable for high-resolution prototypes.
Challenges in Rapid Prototyping with Plastic
While the advantages of rapid prototype plastic are substantial, several challenges must also be addressed:
- Material Limitations: Not all plastics are suitable for all applications, and sometimes rapid prototypes do not perfectly replicate the properties of the final product.
- Surface Finish: Prototypes may require post-processing to achieve a smooth finish, which can add to the time and costs involved.
- Dimensional Accuracy: Although modern rapid prototyping technologies are precise, achieving perfect dimensions can sometimes be challenging.
Best Practices for Successful Rapid Prototyping
To fully leverage the benefits of rapid prototype plastic, consider the following best practices:
- Choose the Right Material: Assess the requirements of your prototype carefully. Selecting the right plastic based on mechanical properties, flexibility, and durability is crucial.
- Iterate Designs: Utilize the rapid prototyping process to refine your designs continuously. Embrace the ability to iterate and improve upon your prototype instead of settling for the first version.
- Involve Stakeholders Early: Gather feedback from team members and potential users early in the process to ensure that the prototype meets all necessary requirements.
- Work with Experts: Partnering with a professional service provider like Deep Mould can enhance the quality of your prototypes and ensure they meet industry standards.
Deep Mould’s Expertise in Metal Fabrication
As part of the invaluable landscape of modern manufacturing, companies like Deep Mould specialize in metal fabrication and understand the critical role of rapid prototyping. By integrating advanced prototyping techniques with their metalworking expertise, they provide clients with tailored solutions that can dramatically reduce lead times and increase productivity.
The Intersection of Metal Fabrication and Rapid Prototyping
Metal fabricators have begun to adopt rapid prototyping techniques to create immediate models of metal parts. Through collaboration with rapid prototype plastic techniques, they allow for:
- Enhanced Design Evaluation: By creating plastic prototypes of metal parts, engineers can evaluate designs more comprehensively before proceeding with final production.
- Better Fit and Function Testing: It enables rigorous testing of fit and function, ensuring that the final metal parts will perform as intended.
- Reduction in Waste: Early detection of design flaws helps to minimize material waste during actual fabrication.
Conclusion
In the realm of manufacturing, the rise of rapid prototype plastic is a game changer. As industries continue to push for innovation and speed, understanding and utilizing rapid prototyping technology becomes essential. It not only assists in navigating the complexities of product development but also fosters a culture of creativity and efficiency. Companies like Deep Mould, which specialize in metal fabrication, demonstrate that integrating traditional manufacturing techniques with modern prototyping methods leads to a more streamlined and productive operation.
As we look to the future, the ability to combine the strengths of rapid prototype plastic with metal fabrication will propel industries forward, creating a new era of manufacturing that is as flexible as it is advanced.
For more insights into rapid prototyping and metal fabrication, visit Deep Mould and explore the myriad of services they offer to ensure your projects succeed.